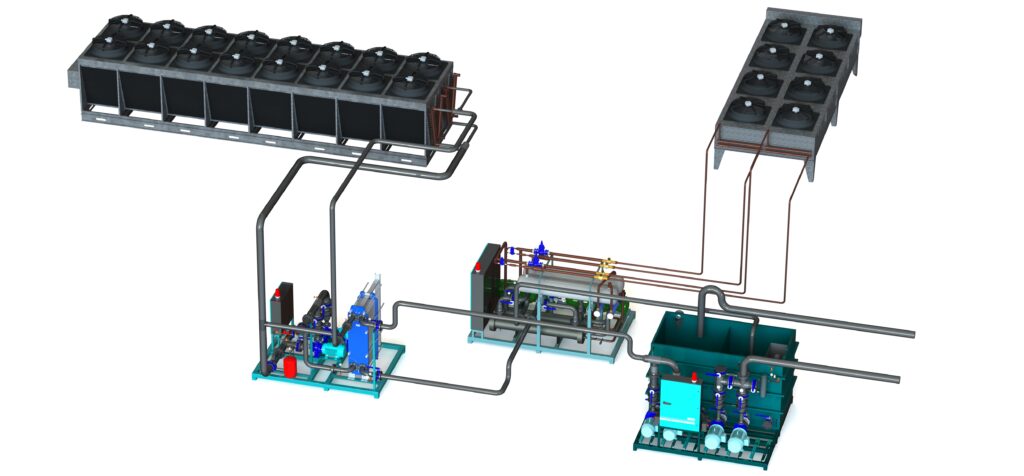
Technical Specifications
Capacity
- Compressor (HP) 20 – 120 or more
- Cooling capacity (Refrigeration tons) 15 to 300 or more
Compressor Options
Semi Hermetic Compressor (WS)
- Semi-hermetic reciprocating compressor
- Suction gas cooled motor
- Suction and discharge stop valve
- Step capacity control
- Crankcase heater with current sensing relay
- Suction and discharge pressure transmitter
- High pressure switch
- Hot gas capacity control
Open Type Compressor (WO)
- Suction and discharge stop valve
- Step capacity control
- Drive coupling and C-flange adaptor/coupling guard
- Suction and discharge pressure transmitter
- Discharge high temperature cut-out
- High pressure switch
- Oil flow switch
- Oil separator with 230 V / Single phase / 50 Hz heater
- Oil heater current relay
- TEFC motor certified for hazardous environments
- Hot gas capacity control
Scroll Compressor (WZ)
- Suction gas cooled motor
- Suction and discharge stop valve
- High pressure switch
- Crankcase heater with current sensing relay
- Hot gas capacity control
Screw Compressor (WQ)
- Suction gas cooled motor
- Suction and discharge stop valve
- Slide valve capacity control
- Integral oil separator with heater and current sensing relay
- Crankcase heater with current sensing relay
- Suction and discharge pressure transmitter
- High pressure switch
- Hot gas capacity control
Evaporator
- High efficiency copper brazed stainless steel plate construction
- designed and constructed in accordance with ASME code
- High efficiency shell and tube construction
- Carbon steel shell (water side)
- Copper tube with inner fin (refrigerant side)
- Vessel designed and constructed in accordance with ASME code
*other materials of are construction available upon request
Water-Cooled Condenser
- Heavy construction while maintaining maximum heat transfer
- Steel shell on refrigerant side
- Copper tubing with outer fin on water side
- Removable heads for cleaning
Stainless Steel Tank
- Baffled Stainless Steel type 304 Reservoir, 11 gauge
- Reinforcement bands
- Removable stainless steel cover
- Overflow connection
- Bottom drain connection with shut‑off valve
- Automatic float operated water make‑up valve
- Thermometer with well
- Spare well opening
- Closed cell flexible insulation nominal ½” thick applied to bottom and sides of tank
Centrifugal Pump Assembly
- Evaporator pumps circulate water from the hot well to the chiller and back to the cold well. This provides a constant flow and pressure for stable operation, maximum efficiency and safety.
- Process pumps circulate water from the cold well to the process and back to hot well. This flow may fluctuate without affecting the flow through the chiller.
- Optional combined standby pump, complete with valved header assembly is capable of acting as either the chiller or process pump if necessary to prevent any unnecessary shut-downs due to an operating pump fault.
- Dedicated standby also available
Pump assembly includes:
- Close coupled TEFC motor
- non-overloading impeller
- Cast iron volute
- Brass shaft sleeve
- Mechanical seal
- Suction shut‑off valve
- Discharge flow/shut‑off valve
- Discharge check valve
- Discharge pressure gauge
Reservoir Mixing Tank and Frame
- Frame manufactured from heavy gauge structured steel tube with welded construction.
- Tank models manufactured from heavy gauge stainless steel.
- Tank cover manufactured from stainless steel and supplied in sections for ease of removal and access ( Covers are optional ).
- All tanks have baffled compartments if required.
- Make-up float valve.
- Tanks are structurally supported around top and sides as required.
Fluid Cooler
- Available as either dry or adiabatic for added cooling capacity
- Heavy duty construction with maximum heat transfer
- Seamless copper tube mechanically expanded into the aluminium fins making permanent metal-to‑metal contact
- All galvanized construction for outdoor operation
- Self-contained controller for fan cycling to maintain set point.
- Coils are manufactured using seamless, deoxidized, heavy wall, smooth copper tubes
Electrical
- 460 / 575 / 230 / 380 Volts 60 / 50 Hz
- 120 / 240 Volt single phase control voltage
- Microprocessor controller
- Operating and fail lights
- UL or CSA approved components
Central Control Electrical Panel
A custom electrical control panel allows one point hookup and may include:
- HMI (Human Interface Device) touchscreens
- PLC (Programmable Logic Control)
- SCADA (Supervisory Control And Data Acquisition) communication systems
- 24/7 alarm reporting to beepers or cell phones
Safety Controls
Tested under load conditions prior to shipment
All safety controls are factory set and checked
- Freeze-up controls
- High and low refrigerant pressure controls
- Compressor motor overload protection
- Tank low-level cutout (glycol units)
- Oil pressure safety control
- Refrigerant pressure relief valve
All pump starters, fuses, disconnect, control voltage transformer, run and fail lights, are housed in a common NEMA rated panel.
Central Thermostat Control System
This system is used to control the chiller units in a multiple central chilling system. The temperature controller is located at the Berg tank and senses the process water temperature. The process water temperature is maintained by cycling the chiller units.