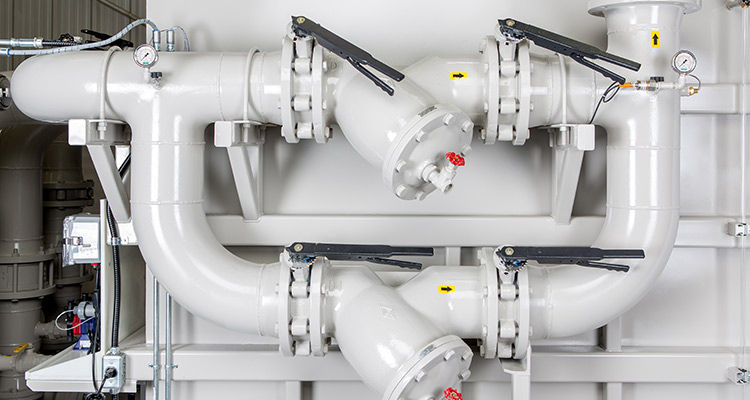
Legislative requirements, coupled with the rising cost of refrigerants—both financial and environmental—call for the chilling system industry to perform safe, and efficient methods of refrigerant recovery. In this article, we look at the most common refrigerant recovery methods used and why they are necessary. We also aim to provide operators with useful tips for servicing chilling system equipment in an efficient and environmentally-friendly way.
Why Recover, Recycle, and Reclaim Industrial Refrigerants?
Since the introduction of the Clean Air Act of 1990 and the Montreal Protocol Treaty, the industrial refrigeration industry has been required to recover, recycle, and reclaim refrigerants or face hefty government fines. Whether in gas or liquid form, synthetic refrigerants can have a damaging impact on the environment.
When chilling equipment and refrigeration systems are being serviced or replaced, the release of synthetic refrigerants into the atmosphere can have a harmful, lasting effect on the ozone layer. In addition, disposing of the liquid refrigerant at a disposal facility permanently alters the chemical makeup of the soil. This is why Canada, along with many other countries, has begun taking measures to limit the use of refrigerants in order to preserve our environment and keep our communities safe.
Reclaiming and reusing refrigerants can also save money over time. Due to the lasting environmental impact of refrigerants, as outlined above, it is becoming increasingly more expensive to replace and to dispose of refrigerants. Industrial refrigeration system operators can improve their bottom line by ensuring that safety guidelines for refrigerant recovery are practiced and observed when servicing or replacing their equipment.
Methods of Refrigerant Recovery
There are three basic methods for reclaiming and reusing refrigerants in chilling systems:
1. Liquid Refrigerant Recovery
This refers to the ability to transfer refrigerant while it is still in the liquid state. This method is especially good for transferring refrigerant from one container to another.
2. Vapour Refrigerant Recovery
The refrigerant is removed in a vapour state. The vapour is then condensed into a liquid form by the recovery unit, and finally, transferred to the recovery cylinder.
3. Push-Pull Refrigerant Recovery
This method is used for transferring large volumes of liquid refrigerant—usually greater than 20 pounds of refrigerant. The recovery unit “Pulls” vapour from the recovery cylinder and produces a high-pressure discharge gas that “Pushes” liquid out of the system and back into the recovery cylinder.
Best Practices for Refrigerant Storage Cylinders
Regardless of which refrigerant recovery method you choose, having the appropriate size and quantity of storage cylinders on-site during the process is key.
- Refrigerant types should never be mixed and/or stored together. Combining R22, R134, R410 or other refrigerants can yield unexpected results. (If you are unsure of the purity of your refrigerant, submit a sample to an AHRI certified lab for most accurate results.)
- Storage tanks must never be filled beyond 80% capacity. Also, the weight capacity for each depends on the type of refrigerant used.
Below is a quick reference chart to show the maximum amount of refrigerant that can be stored in a 30 lb or 50 lb cylinder tank depending on the refrigerant type.
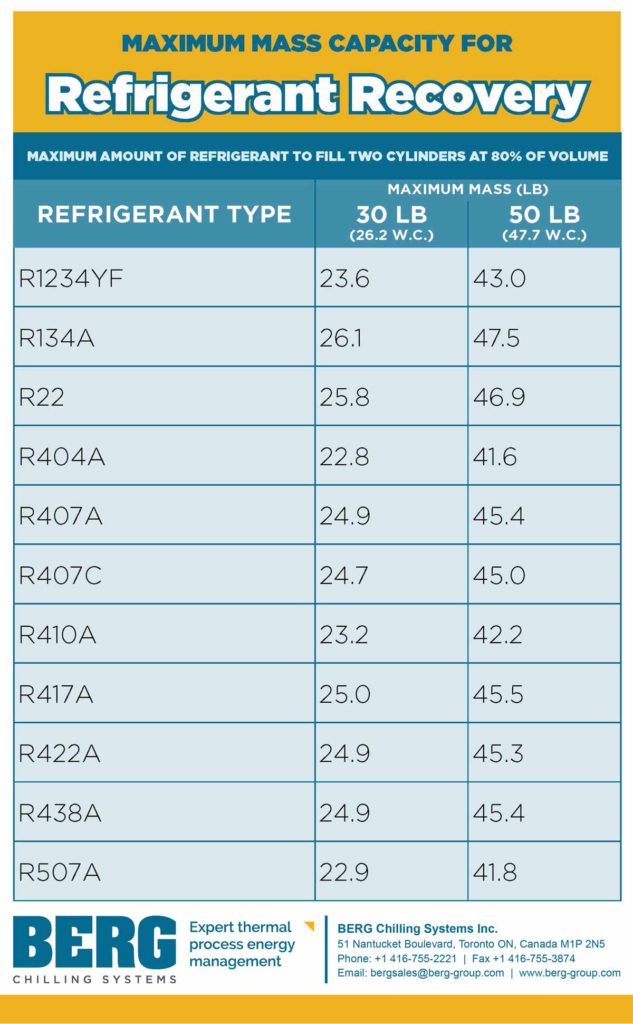
10 Important Safety Practices for Recovering Refrigerants
- Always follow safety precautions: wear goggles, safety equipment, and gloves when servicing chilling equipment and reclaiming refrigerants.
- Never guess the quantity or type of refrigerant used.
- Be cautious when connecting gauges. Low-side gauges can become damaged by over-pressuring from high-side pressure liquid or vapour.
- Don’t assume you know how the unit works. Be sure to read the operating instructions for the specific recovery machine you are using. Each unit’s instructions will differ by manufacturer.
- Always use a machine with a high vapour recovery rate. Vapour recovery can account for up to 80% of the process.
- Avoid using long hoses. The shorter and wider the hose, the faster the refrigerant will be removed.
- Always remove liquid first. After this has been completed, work to eliminate the vapour.
- Don’t expose your recovery machine to harmful elements. Always use an inline filter at the inlet port to keep out slivers to avoid internal damage.
- Always remember to purge your recovery equipment between jobs.
- Don’t forget to check the recovery tank certification. It must be recertified every 5 years.
If you would like to learn more about environmentally-friendly refrigerant solutions for chilling systems, such as refrigerant recovery, or to request service for your industrial refrigeration equipment by a licensed technician, contact Berg Chilling Systems today.